The Importance of Selecting the Right Oil Seals Manufacturer
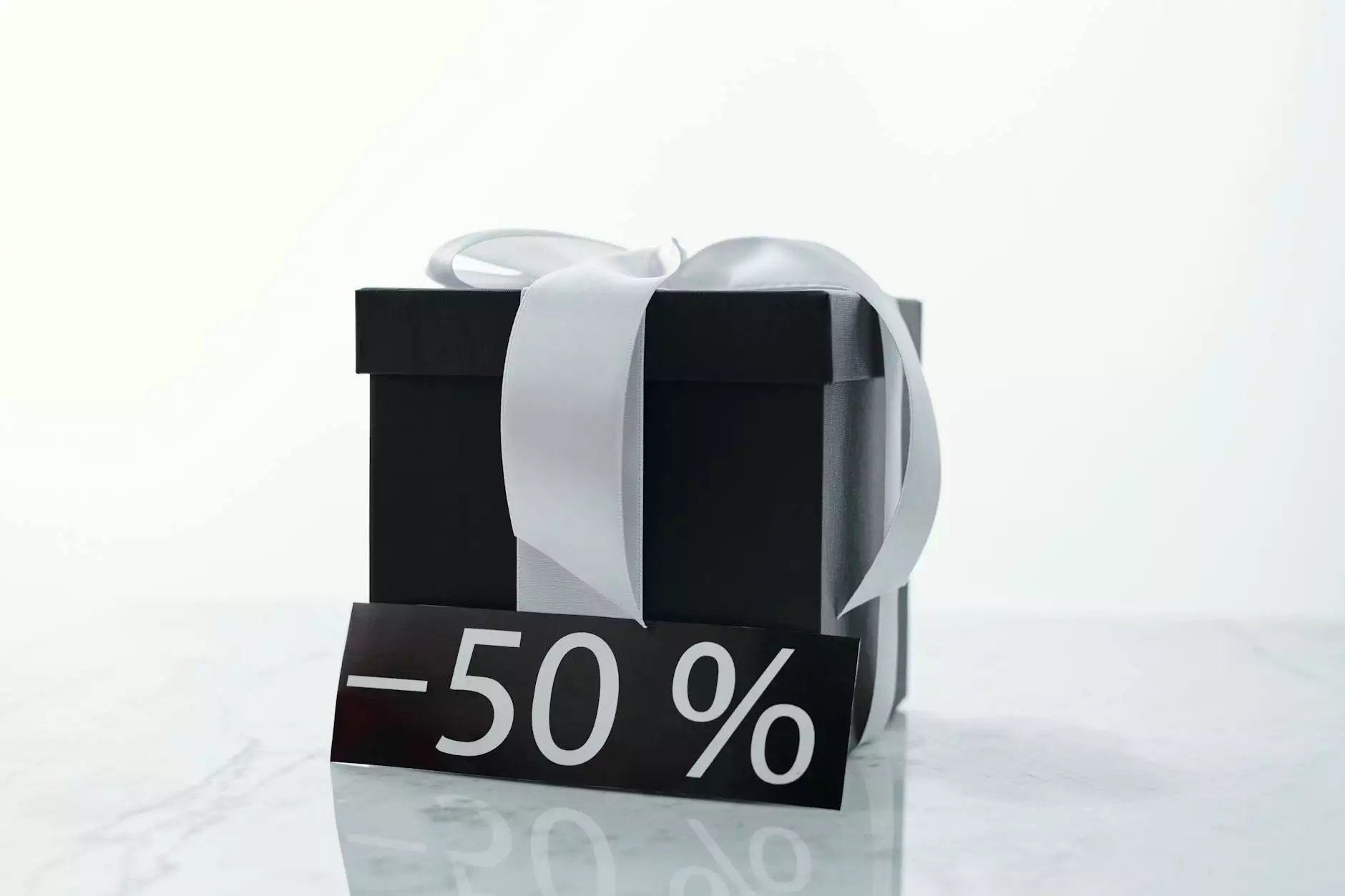
In the realm of industrial components, the role of an oil seals manufacturer cannot be overstated. Oil seals are crucial components used in various machinery, serving to prevent leaks and maintain the efficiency of operations. They play a vital role in a multitude of applications, from diesel engines to hydraulic systems. Understanding the intricacies of oil seals and their manufacturing process can dramatically enhance operational longevity and performance.
What Are Oil Seals?
Oil seals, often referred to as sealing rings, are mechanical devices designed to seal the gap between stationary and moving parts in a machine. They serve multiple purposes, including:
- Preventing oil leakage
- Maintaining lubrication within equipment
- Protecting against contaminants such as dirt and moisture
Applications of Oil Seals in Diesel Engines
In industries where diesel engines operate under high-stress conditions, the integrity of oil seals becomes paramount. Here are some common applications:
- Engine Crankshaft Seals: These seals prevent oil from leaking out of the engine and protect the crankshaft's operation.
- Camshaft Seals: They ensure that the camshaft remains lubricated while sealing off engine cylinders.
- Transmission Seals: Proper sealing in the transmission prevents the loss of hydraulic fluid essential for smooth gear shifting.
Why Choosing the Right Oil Seals Manufacturer is Vital
As a business operating in industries reliant on heavy machinery, collaborating with a reputable oil seals manufacturer is essential for several reasons:
1. Quality Assurance
When the quality of oil seals is guaranteed by a reputable manufacturer, it instills confidence in the durability of the machinery. High-quality oil seals are engineered to withstand extreme conditions, thus preventing premature failure.
2. Expertise and Technical Support
Partnering with an established oil seals manufacturer often provides access to technical expertise. This is crucial for:
- Choosing the right materials
- Understanding design specifications
- Implementing proper installation techniques
3. Customization Options
Every machinery application has unique requirements. A proficient oil seals manufacturer will offer:
- Custom seal designs to fit specific dimensions
- Material options for varying environmental conditions
- Flexible production quantities based on demand
Factors to Consider When Selecting an Oil Seals Manufacturer
To ensure you select the best manufacturer for your needs, consider these essential factors:
1. Industry Experience
Look for manufacturers with a proven track record in producing oil seals for the diesel engine industry. Experience often translates to better quality and reliability.
2. Certifications and Standards
Verify that the manufacturer adheres to industry standards and holds relevant certifications. Compliance with standards such as ISO ensures that the products meet specific quality benchmarks.
3. Customer Reviews and Reputation
Research past customer feedback and the overall reputation of the manufacturer. Satisfied customers are often a good sign of reliable products and services.
The Manufacturing Process of Oil Seals
The production of oil seals involves a meticulous process. Here’s a breakdown of the typical manufacturing stages:
1. Material Selection
Choosing the right materials is crucial, as oil seals can be made from rubber, silicone, or polymer compounds. The chosen material must withstand specific temperatures, pressures, and chemical exposures.
2. Design and Engineering
After selecting materials, the next step involves engineering oil seals to meet the required specifications, ensuring proper dimensions and sealing capabilities.
3. Production Techniques
Advanced manufacturing techniques such as injection molding, compression molding, or extrusion are employed, depending on the design and materials used.
4. Quality Control
Quality assurance protocols are implemented throughout the production process. Testing for dimensional accuracy, sealing efficiency, and material durability is crucial to ensure reliability.
Benefits of Using High-Quality Oil Seals
Investing in high-quality oil seals provides multiple benefits, including:
- Reduced Maintenance Costs: Reliable seals can significantly decrease the frequency of maintenance and component replacements.
- Enhanced Performance: High-quality seals ensure that machinery operates efficiently without interruptions.
- Extended Equipment Lifespan: Proper sealing mechanisms prevent wear and tear, contributing to longer equipment life.
Future Trends in Oil Seals Manufacturing
As industries evolve, so does the approach to manufacturing oil seals. Some emerging trends include:
- Advanced Materials: Research into new materials that provide better resistance to extreme conditions.
- Sustainability: The push for eco-friendly manufacturing practices and materials.
- Automation: Increased use of automation in the production process to enhance efficiency and reduce costs.
Conclusion
In summary, choosing the right oil seals manufacturer is paramount for ensuring the longevity and efficiency of your diesel engines and industrial machinery. By focusing on quality, expertise, and the right manufacturing processes, businesses can significantly enhance their operational capabilities. Trust in a reliable supplier, such as client-diesel.com, who understands the complexities of diesel engine parts and spare parts supply, to meet all your oil seal needs.
Investing in high-quality oil seals is not just a smart decision; it is a necessity for maintaining the efficiency and productivity of your equipment. As you navigate your options, remember to consider the manufacturer’s reputation, experience, and the quality of materials they use.