Exploring the Role of **Pressure Die Casting Machine Manufacturers** in Modern Manufacturing
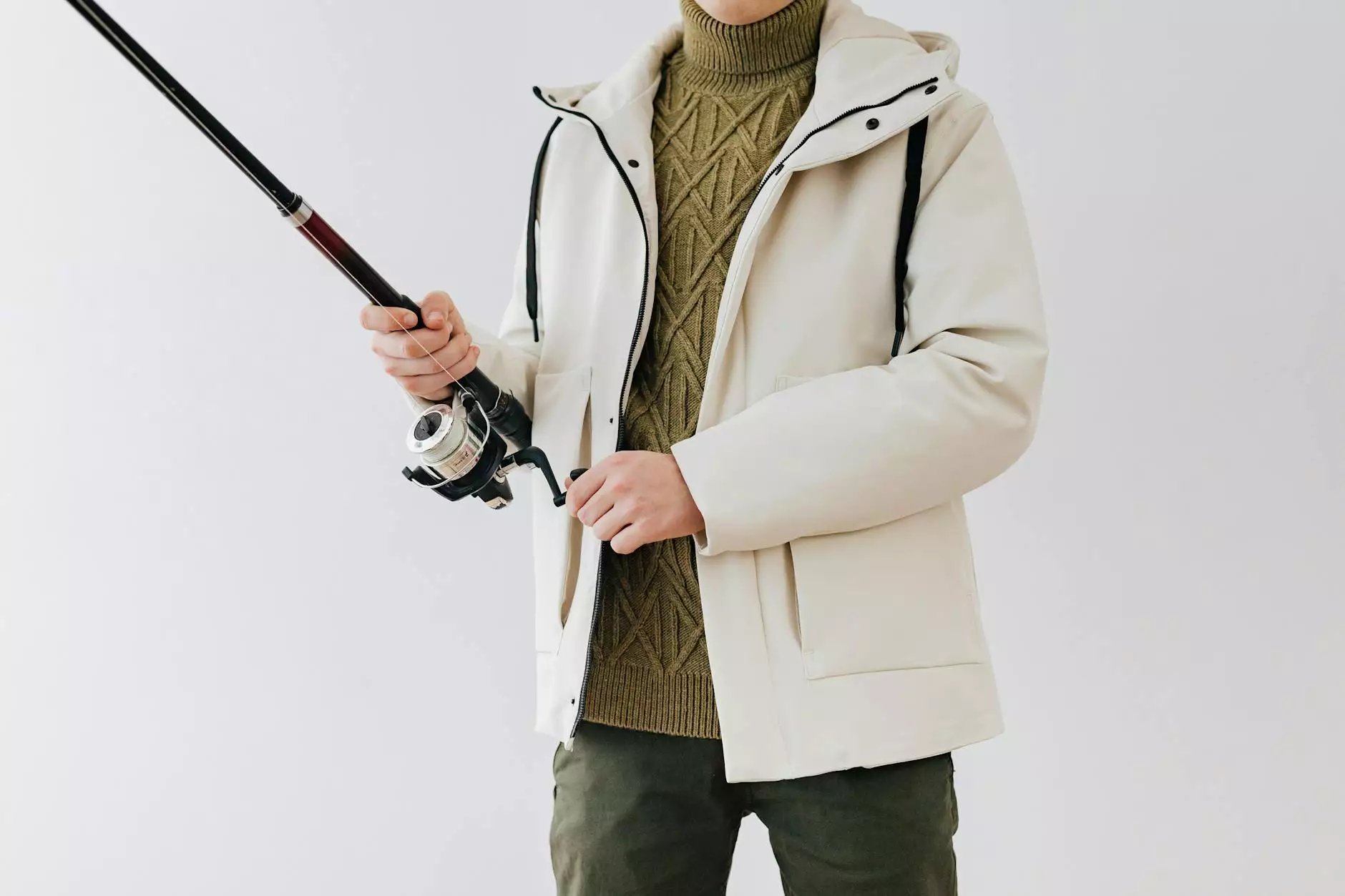
The manufacturing industry continually evolves, driven by technology, innovation, and the need for efficiency. Among its many facets, pressure die casting stands out as a crucial process in creating precision metal parts. This article delves into the realm of pressure die casting machine manufacturers, examining their impact on the industry, the benefits of their machines, and the future trends shaping metal fabrication.
What is Pressure Die Casting?
Pressure die casting is a metal casting process characterized by forcing molten metal under high pressure into a mold cavity. This technique allows for the production of parts with excellent dimensional accuracy, surface finish, and the ability to produce complex shapes. Unlike traditional casting methods, where gravity is the primary force, pressure die casting utilizes hydraulic or mechanical pressure to fill the mold, significantly enhancing production efficiency.
Benefits of Pressure Die Casting
The advantages of pressure die casting are numerous, making it one of the preferred methods for producing metal components:
- Precision: The process delivers parts with tight tolerances and fine surface finishes, minimizing the need for post-casting machining.
- High Production Rates: Pressure die casting can produce a large number of identical parts quickly, making it ideal for mass production.
- Material Efficiency: The method reduces waste, as the amount of scrap generated is minimal compared to other casting processes.
- Versatility: Suitable for a wide range of alloys, including aluminum, zinc, and magnesium, thus providing flexibility in material choice.
Understanding Pressure Die Casting Machines
At the heart of this process are the pressure die casting machines, engineered to perform under intense conditions while maintaining operational reliability. These machines vary in size and complexity, but they generally consist of the following key components:
- Injection System: Where the molten metal is injected into the mold at high speeds.
- Mould Assembly: Consists of two half-molds, typically made of hardened steel, designed to withstand high pressure and temperatures.
- Clamping System: Holds the molds together during injection; integral to maintaining dimensional accuracy.
- Cooling System: Cools the metal part immediately after forming to solidify it quickly, improving production speed.
The Role of Pressure Die Casting Machine Manufacturers
Pressure die casting machine manufacturers play a pivotal role in the industry by designing, producing, and supplying these essential machines. Their contribution encompasses several facets:
Innovation and Technology Development
These manufacturers continually innovate to enhance machine performance. Incorporating advanced technologies such as:
- Automation: Automating the casting process improves efficiency and reduces the likelihood of human error.
- IoT Integration: Internet of Things (IoT) features enable real-time monitoring and diagnostics, resulting in predictive maintenance and further reducing downtime.
- Energy Efficiency: New machine designs focus on reducing energy consumption, translating to lower operational costs.
Custom Solutions for Diverse Industries
Different industries have unique requirements for metal parts, and pressure die casting machine manufacturers provide custom solutions tailored to these needs. From automotive to aerospace, they collaborate with clients to understand specific demands and engineer machines that meet those specifications.
Major Players in the Pressure Die Casting Industry
Within the competitive landscape of pressure die casting, several key manufacturers have established themselves as leaders in the field:
- Deep Mould: Based at deepmould.net, they are renowned for their high-quality machines and innovative designs tailored for efficiency.
- Fairchild Manufacturing: Offers a wide range of casting solutions, specializing in automation and custom designs.
- Die Casting Engineers: Focused on engineering precision die casting systems with advanced technology integration.
Future Trends in Pressure Die Casting
The future of pressure die casting is positioned towards greater technological integration and sustainability:
Emphasis on Sustainability
With increasing environmental concerns, pressure die casting manufacturers are exploring eco-friendly practices. This includes:
- Recycling Metal Scraps: Implementing processes that recycle waste metal back into production.
- Reducing Carbon Footprint: Transitioning to less energy-intensive operations and exploring alternative energy sources.
Advancements in Materials
Research is ongoing into alloys and composite materials that offer even greater strength and lighter weight, promoting their utilization across various industries.
Conclusion
The role of pressure die casting machine manufacturers is crucial in the evolution of manufacturing technologies. Their commitment to innovation, coupled with a focus on sustainability, positions them at the forefront of industry transformation. As businesses look for efficient and environmentally friendly ways to produce high-quality metal parts, these manufacturers are poised to meet and exceed those expectations, leading the charge toward a more efficient manufacturing landscape.