Understanding LOLER Meaning and Its Importance in Business
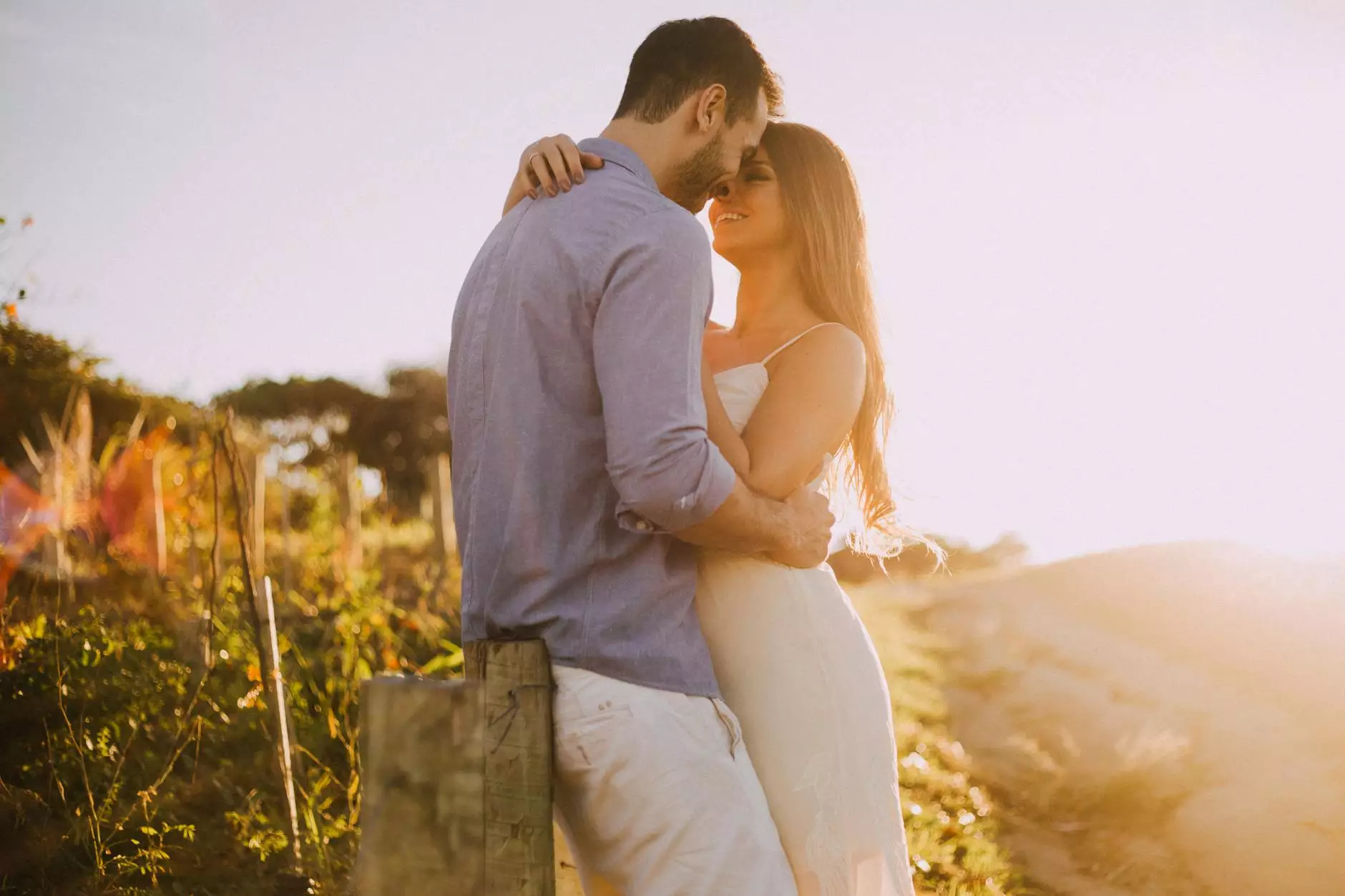
LOLER is an acronym that stands for Lifting Operations and Lifting Equipment Regulations. These regulations were established to ensure safety and compliance in lifting operations across various industries. They are particularly significant in sectors like Home & Garden, Gardening, and Pest Control, where the lifting of equipment and materials is a common occurrence.
What is LOLER?
The LOLER regulations were implemented in the UK to regulate the safe use of lifting equipment. These regulations require that all lifting operations are conducted safely and that the equipment used is suitable for the intended task.
LOLER is an essential part of the legal framework that governs workplace safety. It mandates that all lifting equipment must be:
- Fit for Purpose: Equipment used in lifting must be designed and constructed to meet the requirements of the specific lifting tasks.
- Maintainable: Regular maintenance must be carried out to ensure that the equipment remains in good working order.
- Inspected: Thorough examinations must be conducted at regular intervals to detect any defects that could pose a risk.
The Importance of LOLER in Home & Garden, Gardening, and Pest Control
In sectors such as Home & Garden, Gardening, and Pest Control, safety should always be the top priority. Understanding the loler meaning helps businesses comply with legal standards, ultimately protecting workers and clients alike.
1. Compliance and Legal Obligations
Businesses operating in these industries must comply with LOLER to avoid legal repercussions. Non-compliance can result in hefty fines, increased insurance premiums, and even business closure. Therefore, understanding the loler meaning is not just about compliance but also about sustainable business practices.
2. Ensuring Worker Safety
When lifting operations are conducted without adhering to LOLER regulations, the risks of accidents and injuries significantly increase. Safety measures such as proper training and regular inspections ensure that workers are safeguarded against potential hazards, fostering a culture of safety within the organization.
Key Components of LOLER Regulations
The LOLER regulations comprise several key components that businesses must follow:
- Risk Assessment: Conducting a thorough risk assessment is vital for identifying potential hazards associated with lifting operations.
- Equipment Selection: Selecting the right equipment for the job is critical. Equipment must be suitable for the load and the conditions under which it will be used.
- Training: Workers must receive proper training in the use of lifting equipment, emphasizing safe practices and procedures.
- Maintenance and Inspections: Regular maintenance and thorough inspections are required to ensure all lifting equipment functions appropriately and is safe to use.
- Documentation: Keeping detailed records of inspections, maintenance, and training is essential for compliance verification.
LOLER and Its Impact on Business Operations
Understanding loler meaning is vital for enhancing operational efficiency and safety standards in the workplace. Here’s how it impacts business operations:
1. Enhanced Safety Standards
Integrating LOLER regulations into daily operations elevates safety standards across the board, leading to a safer working environment for employees. This can reduce workplace accidents, leading to lower insurance costs and increased workforce morale.
2. Improved Reputation
Businesses that prioritize compliance and safety establish a strong reputation in their industry. This can lead to better customer relations and increased business opportunities because clients appreciate a commitment to safety and quality.
3. Financial Savings
While ensuring compliance may initially seem costly, the long-term financial benefits often outweigh the expenses. Fewer accidents lead to lower insurance premiums, reducing workers' compensation costs and the potential for equipment damage.
The Process of Implementing LOLER in Your Business
Integrating LOLER compliance into your business operations requires structured planning and consistent monitoring:
1. Conduct a Compliance Audit
Start with a comprehensive audit of current policies and practices concerning lifting operations. Identify areas where compliance with LOLER regulations may be lacking.
2. Develop a Compliance Plan
Based on the audit findings, develop a detailed compliance plan outlining the specific steps needed to align with LOLER regulations.
3. Train Your Employees
Provide training for all employees involved in lifting operations. This training should cover safety procedures, equipment usage, and regulatory obligations.
4. Implement Regular Inspections
Establish a schedule for regular inspections and maintenance of lifting equipment. Document all findings and corrective actions taken.
5. Review and Update Policies Regularly
Regularly review your safety policies and procedures to ensure ongoing compliance with LOLER and address any new risks that may arise.
Conclusion: Safety and Compliance Go Hand in Hand
In conclusion, understanding loler meaning is essential for any business involved in lifting operations, particularly in the Home & Garden, Gardening, and Pest Control sectors. By committing to LOLER compliance, businesses not only safeguard their employees but also enhance their reputation and operational efficiency. The path to compliance may require effort and investment, but the benefits in terms of safety, financial savings, and legal protection are immeasurable.
For businesses like Safe Plant UK, integrating LOLER regulations is a step towards a safer, more responsible future. By adhering to these guidelines, you not only foster a culture of safety but also position your business as a leader in the industry, dedicated to compliance and quality.